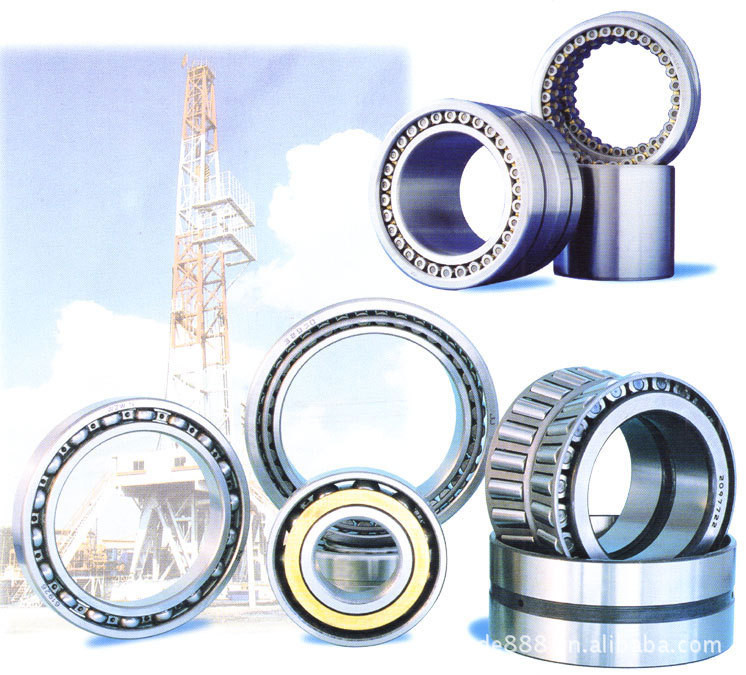
- Oil drilling equipment bearing company
- Petro drill Bearing Mud Pump Crankshaft bearing Frac Pump Bearing
Home> Technical Articles> Analysis and Countermeasures of High Temperature Oil Pump Bearing frequently

- Address1566 Tampines Industrial Avenue 5,Singapore 526818
- Factory Address1566 Tampines Industrial Avenue 5,Singapore 526818
- Phone(Nonworking Time)+6531591338
Analysis and Countermeasures of High Temperature Oil Pump Bearing frequently
2018-11-03 11:14:56Failure cause of 1 oil pump
The oil pump is supported by rolling bearings at both ends. The bearing adopts oil ring self lubrication and natural cooling mode, and the eleven stage pump structure is made of twelve stage pumps.
The pump shell is made of double volute structure, and 10 impeller is arranged symmetrically on the back to back. The eleventh stage impeller adopts the balance of the mouth ring and the balance hole to balance the axial force, and the eleven stage impeller is at the level eleven.
Between the impeller and the five stage impeller, a spiral seal balance sleeve is arranged between the two stages to balance the axial force between the high pressure zone and the low pressure zone. The spiral seal is mainly made of right-handed threads.
Interstage sleeves and supporting interstage rings. When the interstage sleeve and the shaft rotate, the fluid friction acts on the liquid in the spiral groove, causing the axial back pressure, and its value and cavity.
The pressure in the body is equal, so that the liquid leakage can be eliminated and sealed. When the screw thread is gradually eroded to a certain extent, the seal fails.
1.1 common problems of over temperature failures
(1) there are a lot of impurities in the impeller chamber, which are mainly a large amount of rust and a little oil sludge. (2) there are serious wear parts in the pump, and the outlet of the five stage impeller outlet.
The ring is washed out of several deep trenches, and there are many pits in the impeller. There are several deeper grooves between the five stage and eleven stage impeller.
Failure; other impeller pump ring and impeller mouth ring wear and tear seriously. (3) the main pump current has a rapid rise in the temperature of the non drive bearing before the failure occurs.
There has been a marked decline.
1.2 failure analysis
After many disassembly and repair, it is found that there are a lot of impurities in the pump cavity. The spiral seal balance sleeve between the stages is seriously eroded by the impurities in the fluid and is eventually broken down. flat
The balance sleeve is between the eleventh and fifth stages of the pump, and belongs to the labyrinth structure. The labyrinth sleeve plays an axial balancing role when relative rotation occurs, and the oil pressure is about 10MPa. Oil flow
The direction is opposite to the inner and outer sleeves. Due to the high pressure and the small and hard granular impurities in the liquid, the shot peening phenomenon occurs.
Granular impurities penetrate the balance sleeve, causing the balance sleeve to lose its effectiveness. The axial imbalance force of the pump acts entirely on the thrust bearing, resulting in overdrive of the non drive thrust bearing.
。 Therefore, the root cause of the failure of the oil pump is the impurities in the oil, especially small and hard granular mechanical impurities.
Shot blasting.
1.3 impurities in pipes
The impurities in the product pipeline mainly come from two aspects: the mechanical impurities such as welding slag and sediment left in the pipeline during construction, and the corrosion products in the pipeline. Yes.
The sediment samples from the oil pumping station were sampled and analyzed, and the sediments were mainly composed of non organic components, accounting for 90% of the total sediment.
After sampling and analyzing and detecting the impurities after each pump disintegration, the organic components are mainly linear saturated hydrocarbons with large molecular weight, which are identical with those of the finished products.
The main component of inorganic component is iron containing substance formed by corrosion of steel tube, and contains a small amount of manganese nickel and soluble calcium and magnesium components. X- ray fluorescence spectra of some samples were carried out.
The impurities in pipeline oil are mainly composed of rust and oil sludge. In dry air, a layer of oxide film is formed on the steel surface at room temperature.
The oxidation reaction inside the tube can be inhibited effectively. If there is water vapor in the atmosphere, the water film will be attached to the surface of the steel. If there are substances such as carbon dioxide and hydrogen sulfide in the air,
The water film on the pipe surface becomes weak acid, which aggravate the corrosion of the steel surface. Through the test of the internal rust of the steel tube, the impurities in the pipeline are left behind in the pipeline construction.
Sand and rust on the inner surface of pipes.
To sum up, the failure of the oil pump should be caused by a large number of impurities in the oil product (the rust of the inner wall of the steel pipe) and the frequent shot blasting erosion of the interstage sleeve.
2 solutions
The side ring of the upgrade bushing bushing and the corresponding fifth stage impeller mouth ring are corresponding to the side material, and the hardness is adjusted from 170 to 210HB to 220 to 240HB, and the erosion resistance is enhanced.
Adjust the mesh number of filter net, strengthen the filtration and collection of impurities, adjust the filter net from 20 mesh to 30 mesh, and pipe blockage according to filter.
Switching between 20 and 30 items. A new strong magnetic rust removal device is added along the oil pumping station along the line, and it is further installed in the collecting barrel.
The separation effect of mechanical impurities in oil. According to the blockage of the filter, the pigging operation is carried out in a targeted manner.
。 According to the characteristics of liquid-solid conveying, when a large amount of impurities in the pipe are actively disturbed by the oil head, the large number of impurities in the pipe will be introduced into the main pipe with oil flow. Impurity accumulation along the oil
The direction of flow is increasing, especially the terminal is the blind end, which accumulates the largest accumulation and is most seriously affected by oil flow disturbance.
In addition, the stability of the system will slowly precipitate along with the stable working conditions after the start-up and operation conditions are stable, and the impurity entrainment will be greatly reduced.
Transport characteristics, oil flow will produce clear mixing stratification. When parallel operation (the main station is a parallel operation of two pumps), the operation combination should be carried out when multiple pumps are combined.
In the front of the machine, the pump first inhaled more clear layers. According to the direction of the oil flow, the oil flow cuts into the vertical straight pipe section of the pump inlet (which is similar to the cyclone separator).
The tangential separation of impurities in the oil flow falls into the mother pipe by gravity, and then flows into the subsequent pipeline with inertia.
